Developer interviews
It is possible to suppress glare and the reflection of external light at the same time.
Low-reflection film
Q. What kind of product is a low-reflection film?
And what applications are this kind of films used for?
Low-reflection film is used on the top surfaces of displays to prevent light reflection (AR: Anti-Reflection, LR: Low-Reflection). Applying this film to the top surface of the display helps to suppress any reduction in visibility due to external light such as sunlight and lighting reflected by the screen.
Examples of places where our low-reflection film is used include the center information display (CID), which is the large display located in the center of the automotive dashboard, and the digital meters (meter cluster) that contain the instruments. If the reflection of outside light is not properly suppressed, visibility will suffer, hindering driver safety and making driving less comfortable.
In recent years, along with displays becoming larger and more numerous, with higher definition and improved image quality, in-vehicle displays have also become more diverse in their designs. However, prioritizing design can compromise visibility. For example, until recently, there was a visor (cover) over the digital meter display screens that protected them from exposure to strong direct sunlight. However, this is increasingly being removed for the sake of design improvement (becoming visor-less displays).
Without a visor, the display becomes more susceptible to outside light, reducing its visibility. Using our low-reflection film suppresses the reduction of visibility and contributes to a safer drive.
Q. What are the advantages of using low-reflection film?
Using our low-reflection film suppresses the reflection of external light, thereby reducing glare and preventing reduction of the visibility of in-vehicle displays. It also gives resistance to fingerprints and scratches, so the fingerprint smudges left when operating a touch panel are easy to wipe away, and the panel is protected from scratches when it’s wiped. Furthermore, if a touch panel is made of glass, there is the risk of it shattering in a collision. However, because this film is shatter-resistant, applying it to the touch panel helps prevent fragments from scattering.
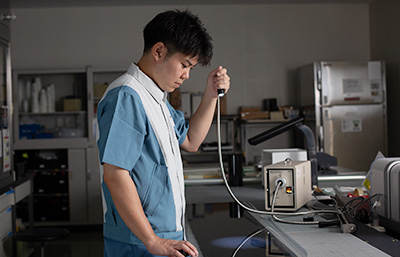
Q. What are Lintec's strengths in low-reflection film?
To date, we have developed various functional hard coat films and adhesive products for the display industry. By leveraging our experience and knowledge cultivated over many years, we are able to offer films with optimal functionality.
The low-reflection film forms a thin coating on the surface of the film substrate, with low-reflection functionality achieved by adjusting the refractive index and the thickness and by the addition of fine particles. In addition, by combining the film with an AG (Anti-Glare) layer that is compatible with high-definition screens, it is possible to suppress glare and the reflection of external light at the same time.
We also boast an integrated production system that includes everything from hard coatings to adhesive processing. In order to use the low-reflection film, an adhesive is needed to attach it to the panel, but since we are able to perform adhesive processing in-house, we can provide our low-reflection films in adhesive-processed configurations. The adhesive can also be given transmittance control, diffusion, and UV absorption properties.
Q. Please share how difficult and interesting it is to Research and Development.
As we lowered the reflectivity, it proved difficult to also have it resistant to scratches and fingerprints.
In addition, it was very difficult to establish processing conditions because a coat layer with a thickness of about 100 nm was being formed on an AG layer that has an uneven surface. After many rounds of prototyping and discussions, we were finally able to establish the conditions needed to achieve uniform performance. It was a real relief when the low-reflection film was finally adopted and mass-produced.
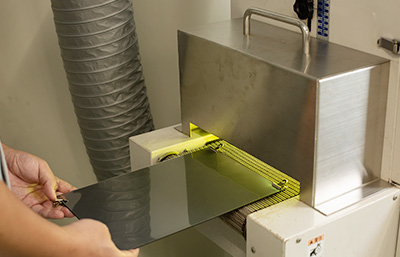
Q. What upcoming challenges and developments are you working on now?
In the market, glass tends to be preferred as the cover material for the display top surface in terms of visibility and texture.
However, there are safety concerns, such as glass breaking on impact, so films that look like glass offer both design and safety advantages.
Our aim is to create hard coat films that, after being laminated to panels, look and feel as close to glass as possible.
We also foresee more displays being installed in automobiles due to the increasing popularity of new energy vehicles and autonomous driving functions.
In the future, displays will continue to become more multi-functional, creating more needs than ever. We plan on taking this challenge head-on by developing new technologies to meet the market’s needs.
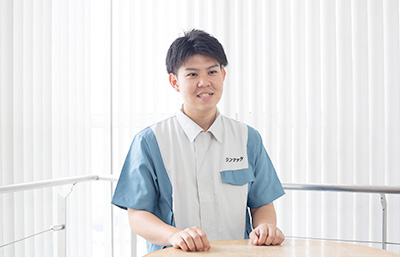